ALUMINIUM DIP BRAZING
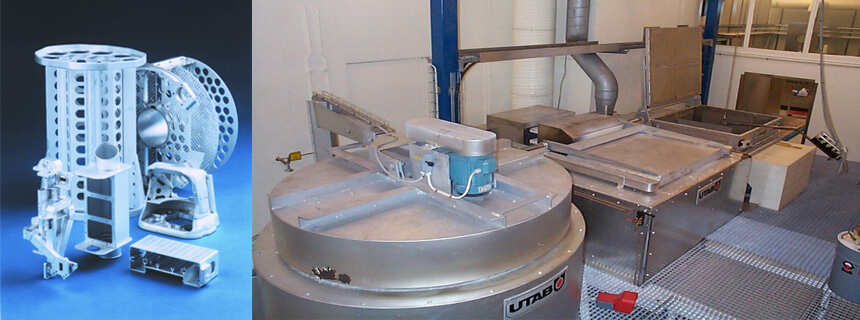
Aluminium dip brazing is a method of brazing aluminium alloys. It was
developed in the U.S. during the 1950's mainly to join waveguide
components for radar equipment. Today's primary use of the technology
is for manufacturing heat exchangers for the cooling of electronics and
for rapid prototyping of high precision components. Dip
brazing is often the more economical alternative to casting/moulding
when developing components for smaller series. Today we work with
companies within the defence and medical industry but we also work on
custom projects where the client requires the possibility to quickly test the
durability/strength/load and construction of a component.
Swedish standard for soldering is FSD 5155
American standard for soldering is MIL-B-7883
Dip brazing's advantages are many, including:
• Even heating of the entire piece
• No risk of burn-through or melting of the base material
• A large number of joints can be joined simultaneously
• Soldering of normally hard to reach joints
• Reliable and reproducible joints with high quality, small
joint radii and even surfaces.
• Substantially shorter lead times
• Very good joint strength
• Cost effective